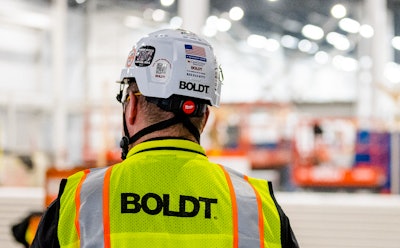
The Boldt Company is setting a new standard for worker safety on its project sites. Having transitioned from hard hats to safety helmets for its employees in 2022, Boldt is now extending this requirement to everyone on its sites for the same level of protection.
The construction industry has the greatest number of both fatal and nonfatal traumatic brain injuries (TBIs) among U.S. workers resulting from falls or struck-by accidents, according to a series of medical research studies highlighted by the US Centers for Disease Control and Prevention (CDC). This strategic shift marks a leap in changing that.
While the construction industry has long adhered to hard hats, the protective gear’s design doesn’t account for frontal, rear or side impact protection. Workers struck in one of these areas are more at risk for concussions or serious TBIs that affect both long-term physical and mental health. Boldt’s protective stance to safeguard employees across all crafts, including those that require versatile accessories (e.g., grinding, torching, welding and excavating), moved the company to explore options.
Safety Requirements for Head Protection
“Our employees are our most valuable assets, and their safety is non-negotiable,” said Scott Frazer, vice president of Corporate Safety at Boldt. “By making helmets the new norm, we’re ensuring that every worker has the best protection possible. Our goal is to make helmets the undisputed choice for construction crews.”
Boldt first decided to move away from hard hats in 2021. The company researched different helmet and accessory manufacturers and styles, field-testing each option to ensure optimal safety and functionality. Criteria included American National Standards Institute (ANSI) and European Standard (EN) ratings, Type 1 versus Type 2 protection, product specifications such as weight, features and functions, service and shelf life, performance in different regions, weather conditions and trades (e.g., mills vs. mines), cost and more.
Boldt shared its research findings and challenges with the selected personal protective equipment (PPE) manufacturers. It was critical that the chosen manufacturing partners be open to incorporating Boldt’s research findings into their helmet and accessory designs for safety and equipment functionality and meeting craft workers’ needs.
Boldt selected Milwaukee Tool’s Milwaukee BOLT Safety Helmet along with PPE manufacturer Jackson Safety’s Hard Hat Interchange System (HHIS) for helmet accessories (e.g., welding attachments, full face shields, earmuffs, lamp clips, ear plug hooks, wind, rain, cold weather and sun protection, replacement padding, brims, etc.).
Unlike traditional hard hats, the new helmet includes high-density foam to better absorb impact to all areas of the head, an integrated chinstrap to secure it to the wearer’s head, comfortable padded suspension with adjustable swinging ratchet, antimicrobial sweat band and liner, air vents to combat heat stress, accessory slots to integrate additional PPE and accessories to adapt to different work scopes and more. In addition, the helmet offers a five-year service life from the date it is put into service and an extended shelf life of 10 years, two times longer than many traditional hard hats.
Getting feedback from Boldt’s employees helped us develop the Jackson Safety HHIS system that not only works for them but can also be used throughout the industry,” said Mark Nelson, Jackson Safety. “I’d highly encourage other companies to implement proactive programs like Boldt has that have an immediate positive safety impact on their employees.”
Long-term Solutions
“I appreciate the team working hard to find solutions for everyone in the field,” said Andrew Olson, journeyman ironworker and Boldt foreman. “The Boldt safety team worked to find the best fit for hot work accessories with the resources that were available to them because there weren’t a lot of options when we made the switch. I know getting everyone on the same page from hard hats to helmets was not easy, and anytime I called with a question or problem, they got on it right away.”
Boldt recognizes the cost implications of the transition, with helmets more than two times the cost of traditional hard hats. However, the company emphasizes that the investment is a small price to pay for the long-term well-being of its workforce.
“The transition to helmets is a strategic one with far-reaching benefits. We’re ready to collaborate, share insights, and work collectively to make helmets the standard across the industry,” added Frazer.