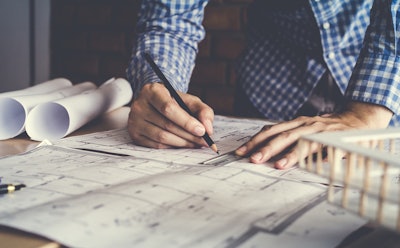
Yet construction projects tend to be anything but simple. Highly litigious and often fraught with delays and disputes, overruns – both schedule and cost - are not uncommon in the industry. While delays, disputes, and overruns have always been unwelcome guests in the construction industry, their presence has grown in recent years. The numbers tell a grim tale. Consider these statistics:
- A recent article from Autodesk points to a KPMG study stating that just 31% of all projects came within 10% of the budget in the past three years.
- A LinkedIn article from a construction industry expert stated that 90% of all projects are over budget and behind schedule.
- This is not just a domestic issue: One study cites that the vast majority of construction projects completed in 20 countries over a 70-year period experienced cost overruns, highlighting that the overall average overrun was 28%.
Moreover, the longer the duration of the project and the larger the project’s scope, the more vulnerable it is to risk. Because construction projects involve numerous moving parts and because they usually extend for many years (as is the case with large commercial projects), managing project schedules can become quite tricky, if not excessively complex.
You’ll notice that we made a distinction between cost and schedule overruns. That’s because, while they both affect the project’s final outcome, they do so in different ways. So it’s instructive to understand the difference between these two categories of overruns.
What is a Project Schedule Management Overrun?
A broad definition of schedule overruns is the extra time required to finish a given construction project beyond its original planned duration. To be more specific, when the stipulated completion time of a construction project is pushed forward, the project has experienced a schedule overrun. Consequently, schedule or time overrun is the late completion or late delivery of a project.
Alternatively, cost overruns occur when a project completes at a higher cost than what was budgeted. One or both can occur when managing a project schedule, often occurring at the same time, with one (cost overrun) usually being the direct result of the other (schedule overrun). In other words, while they are completely different animals, they are often inextricably intertwined.
Now that we know what schedule overruns are, how do we avoid them? Here are five practical tips to avoid overruns when managing your construction project schedule going forward.
#1: Hire Expert Designers to Limit or Eliminate Defective Designs Early on
What happens at the genesis of the project can create a world of pain later on down the “schedule line.” Quite frequently, cost overruns result from breaking ground on and executing incomplete project designs and/or deficient designs. These substandard designs inevitably result in substandard work. More importantly, errors made during the design process can have an exponential impact later on during the final phases of the project, as the longer the errors go undetected, the greater the likelihood of rework.
To avoid design deficiencies or errors, employ an experienced and qualified designer to draft highly accurate and detailed designs right from the start.
#2: Check and Manage Your Project Schedule Quality
It’s all about the project schedule. Starting with a sound, high-quality schedule is key to project success and managing – or even eliminating - schedule overruns.
To avoid delays, you’ll want to check and ensure that your initial project estimates, task durations, critical path, planned costs vs. actual, and resources in the project schedule are all within best practices guidelines and acceptable levels before you begin your project.
Start off right and assess the quality of your schedule by checking it against the DCMA 14-Point Schedule Quality Assessment or running it through project-schedule analytic software.
#3: Proactively Manage Rework
According to Construction Junkie, the median cost of rework, as a percentage of total project cost, is roughly 4%-6%, and that is only taking into consideration the direct cost of reported rework. Thus, you should actively work so you don’t have to re-work.
However, if you were not fortunate enough to avoid rework, the best approach is to manage it proactively. Rework - the process of redoing or correcting work that was not performed correctly - is one of the biggest reasons for schedule overruns. Rework can emerge from both project design issues and/or project construction problems. As Kitchell Progress, a publication of Kitchell Corporation, states, “Rework is the single largest biggest contributor to delays, and the time/cost is not recoverable.”
To elude this pitfall and practice quality control, take a proactive approach to build by diligently inspecting, recording, and correcting non-conformances as the work is placed.
#4: Anticipate and Minimize Schedule Change Disruptions
Changes to the project scope and schedule constitute some of the biggest reasons for project schedule overruns in both time and costs. A primary change occurs when an owner or contractor introduces new specs, fixes, or requirements after project documents have been finalized and the schedule is completed. This, of course, results in additional costs to cover the new expenditures and will send budgets soaring.
An article on the website for Bridgit, a workforce intelligence solution for the construction industry, details two excellent ways to avoid and account for change orders. New technology now allows modeling and simulation of various scope changes during the pre-construction phase, which can greatly prepare project managers and schedulers for these risks. Additionally, it’s recommended that project schedulers anticipate and prepare for change allowance. Buffer your construction project schedule against overruns early in the project cycle by allocating adequate resources both in time and cost to compensate for these adjustments.
#5: Navigating Events Out of Your Control
From record-breaking inflation and extreme weather to untenable site conditions and supply chain disruptions, every construction project has been hit with “unforeseen conditions” and ‘extreme event’ surprises adversely impacting their construction project schedules.
While it behooves every project management team to perform a risk assessment for unforeseen conditions and events, modeling can’t possibly forecast every extenuating circumstance. Examples include an unprecedented inflation rate that increases material costs or a viral pandemic and war that introduces schedule overruns largely out of the team’s control.
Approaches like strategic planning, early collaboration, data-driven decision-making, reliable supply chain management, and holding large safety “stores” of stock materials are effective ways to ensure a secure supply chain. Being safe is better than being sorry.
Just as in life, even with the best-laid plans, problems and surprises happen to the most seasoned project schedulers and on the most high-profile construction projects. The question is not whether you will face project crises that cause schedule overruns; you will. Rather, it’s about how prepared you are to respond to them when they occur.
As the expression goes: An ounce of prevention is worth a pound of cure. Using these five tips to manage your project schedule, you will be on your way to successfully avoiding - or at least mitigating - the effects of future schedule overruns.